Vacuum Investment Casting of Oxygen-Free Copper (OFHC): Why Controlling Oxygen Below 10 ppm Is Critical
- Pahwa MetalTech Pvt Ltd
- Apr 4
- 2 min read
In the realm of high-performance electrical applications—where reliability, conductivity, and durability are paramount—Oxygen-Free High Conductivity Copper (OFHC) has established itself as the material of choice. But to unlock its full potential, especially for high-voltage and high-current environments, controlling oxygen levels below 10 parts per million (ppm) during casting is absolutely essential.
At Pahwa MetalTech, we specialize in Vacuum Investment Casting of OFHC copper, achieving oxygen levels of less than 10 ppm. This precision enables us to deliver parts that meet the stringent requirements of the electrical and switchgear industries.
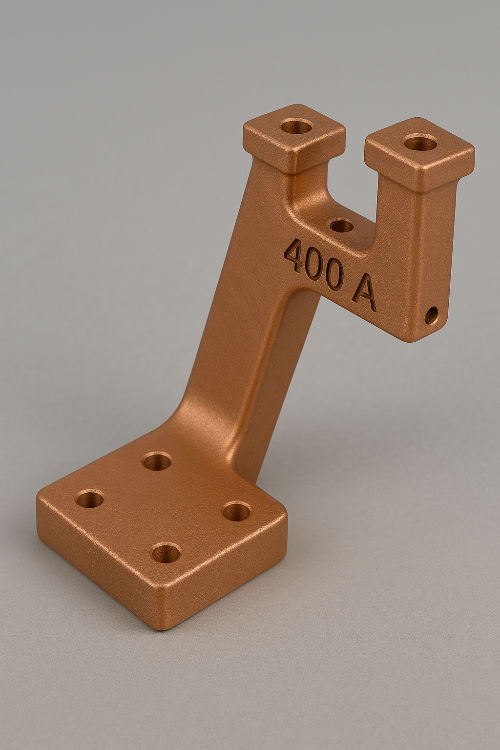
Why OFHC Copper Matters
Oxygen-Free High Conductivity Copper (OFHC) is a high-purity copper alloy with:
> 99.99% copper content
Oxygen content < 10 ppm
Electrical conductivity > 101% IACS
Superior thermal conductivity
Excellent formability and corrosion resistance
Because of its superior properties, OFHC copper is widely used in:
High-voltage switchgear and circuit breakers
Electrical contacts and terminals
Busbars and current collectors
Power semiconductor packaging
RF and microwave systems
The Problem with Oxygen in Copper Castings
Copper is highly reactive with oxygen. During conventional casting methods, even in inert atmospheres, oxygen gets absorbed, forming oxides and impurities such as:
Cuprous oxide (Cu₂O): A non-conductive phase that reduces electrical performance.
Gas porosity: Trapped gases can create voids and weaken structural integrity
Hydrogen embrittlement: Oxygen combines with hydrogen to create water vapor, causing internal cracking during heat treatment or brazing
Just 15–20 ppm of oxygen can degrade the electrical and mechanical properties, making it unsuitable for critical electrical applications.
Vacuum Investment Casting: The Game-Changer
To overcome these challenges, vacuum investment casting is an innovative process capable of delivering the precision, purity, and consistency required for high-performance OFHC copper parts.

Key Benefits of Vacuum Casting for OFHC Copper:
✅ Maintains Oxygen < 10 ppm: Completely eliminates air exposure during melting and pouring
✅ Superior Surface Finish: Ideal for electrical contact surfaces
✅ High Dimensional Accuracy: Near-net-shape castings reduce the need for post-processing
✅ Consistent Metallurgy: No inclusions or impurities, ensuring uniform performance
✅ Complex Geometries: Supports intricate shapes that are difficult to machine
Pahwa MetalTech: Your Partner in High-Purity Copper Castings
At Pahwa MetalTech, we have invested in a state of the art vacuum investment casting facility to manufacture ultra-pure OFHC copper castings with oxygen levels < 10 ppm.
Our Capabilities Include:
Dedicated Vacuum Casting Machines: Sealed chambers prevent oxygen ingress
Custom Tooling & Prototyping: Rapid development and optimization for customer-specific parts
Small to Medium Batch Production: Ideal for precision electrical components
Experienced Engineering Support: From design optimization to final product qualification
Why Sub-10 ppm Oxygen Matters in Electrical Systems
The purity of copper directly impacts the performance of components in high-voltage and high-frequency environments.
Oxygen Level (ppm) | Impact on Conductivity | Suitability for Electrical Use |
> 50 ppm | Significant reduction | Not suitable for high-performance systems |
20–50 ppm | Minor degradation | Risky for critical applications |
< 10 ppm | Optimal conductivity | Required for OFHC applications |
🔧 Looking for Precision OFHC Copper Components?
Let’s talk.
At Pahwa MetalTech, we bring cutting-edge casting technology, deep metallurgical expertise, and a commitment to quality that matches the critical nature of your application.
📩 Contact us at info@pahwametaltech.co.in to explore how our vacuum investment casting solutions .
Comentários